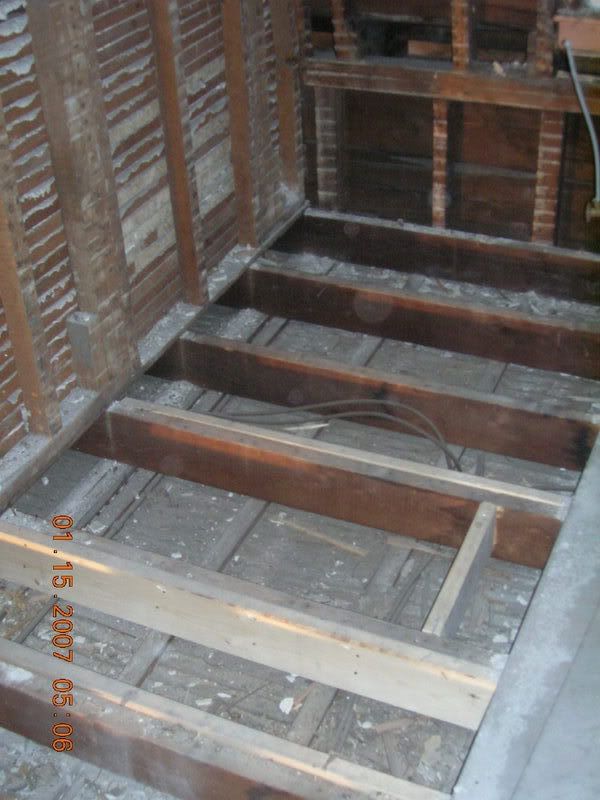
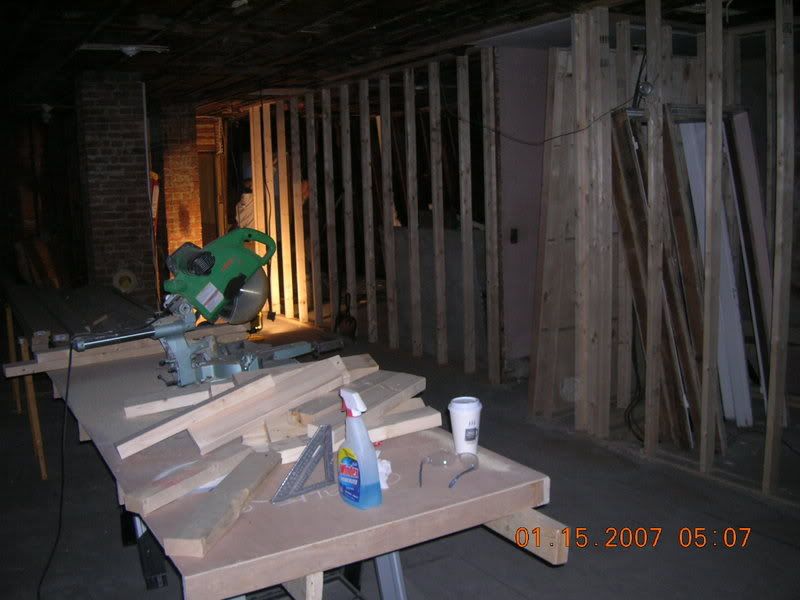
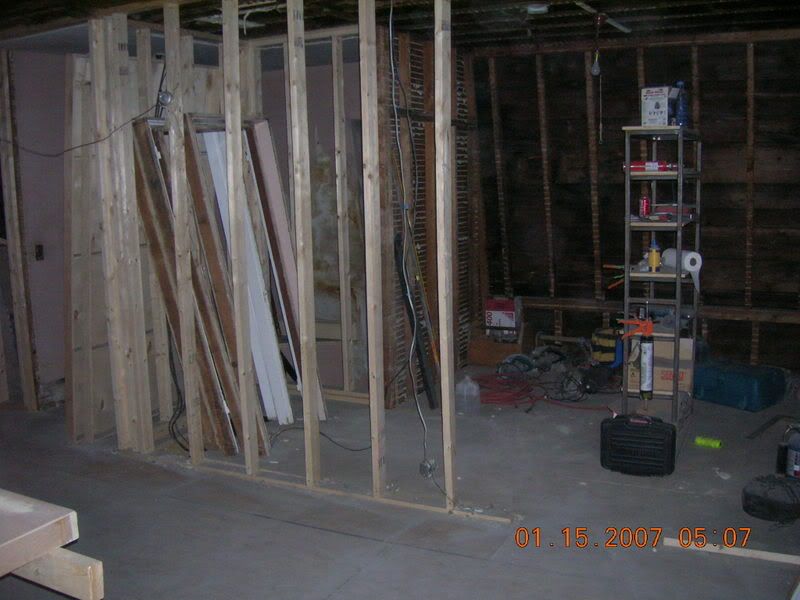
Here you some of the new interior framing. The photo on the right shows what will be the new study. On the left, the line of the study wall is continued past the stairwell to divide the main bedroom from the living and kitchen spaces. The bathroom will be beyond where the light is shining. Ultimately the kitchen and living spaces will be delineated by the kitchen cabinets.
In the meantime, the homeowner wants to get renters into the first floor ASAP. This has involved some basic plaster repair and a fresh coat of paint at the minimum. At the other end of 'minimum' we're installing a new laminated floor in the two small bedrooms and re-finishing the floor of the living room. Part of the dress-up is stripping several coats of lead-based paint from this gorgeous old stone mantle. Yours truly did the honors on that one:

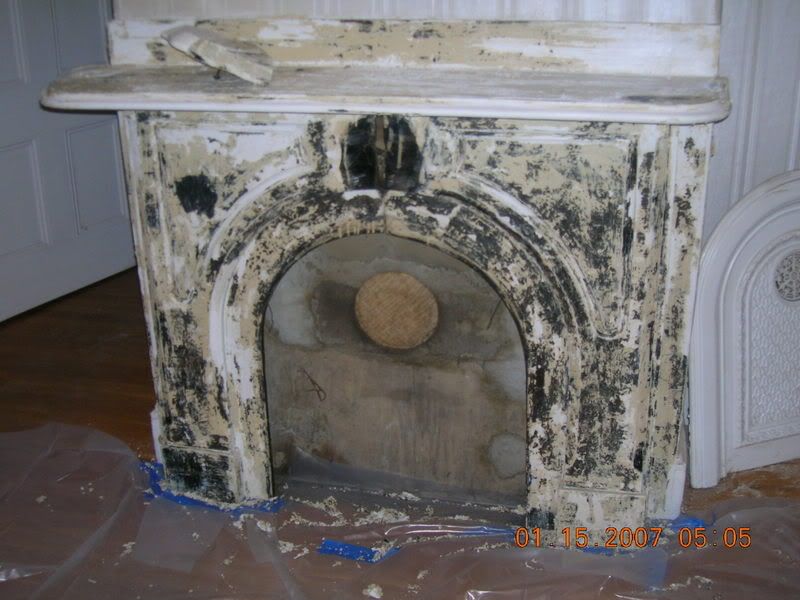
There remains much to do. The outside of the house has some rot and weathering issues and there's to be a new roof covering applied. Upstairs, a skylight in the study and a loft-space extended into the attic. Plus all the finish work. Stay tuned for updates.
Since I'm plugging myself a little bit, here are a couple of photos from a renno I completed in the fall. This old, small barn required significant foundation work and new clapboards. It has new interior framing to support a finished office space on the second floor. The sliding barn door and faux door to the left were one-off pieces I custom made to spec, using recycled antique glass for the panes. The floor off the office is made of recycled barn-boards, planed to a uniform thickness and framed with two courses of yellow pine. I should get some pictures of that, 'cause it looks the business.

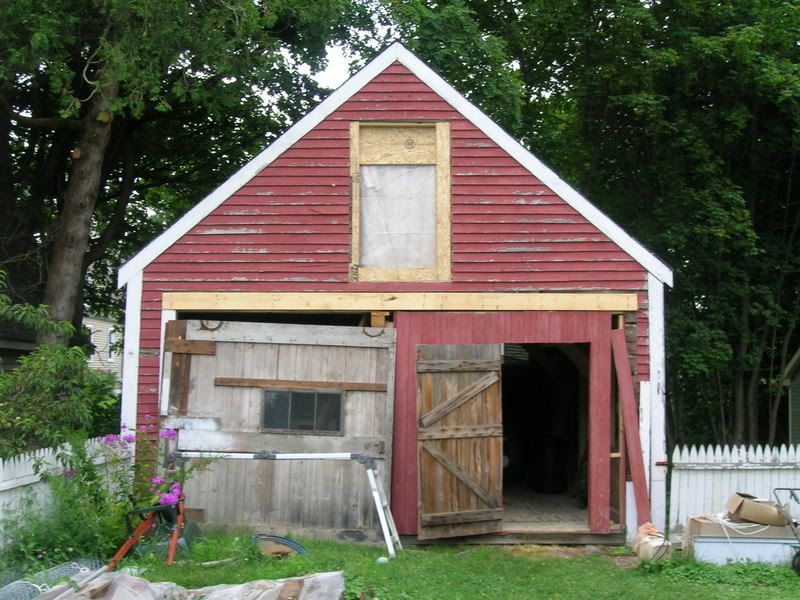
3 comments:
hey dude,
I came across your blog while googling for fire blocking. I'm renovating my 1920's arts-n-crafts house in JP. The building inspector wants me to install fireblocking between the floors to meet code- what material are you using to do it on this project?
James:
As I understand it, 2x material is more than sufficient. The idea (as you might be aware) is simply to stop the chimney effect: the fire-feeding gift that balloon framing gives to us.
On this project, we used old interior-wall studs from the same house that we'd removed to make room for interior re-design. As I'm sure you've discovered, old rough-sawn lumber is a different size than modern KD. The interior framing studs were a dimensional match for the exterior balloon frame, so we were set to go.
The key is to close off the stud bay. So anything that fits snugly between exterior sheathing and whatever you use to cover the inside wall with (plaster and lathe, sheetrock, etc) would work fine. Check with the local building inspector to be sure there isn't a thickness requirement in your area (some places do not allow anything thinner than 2x (1.5"), some places allow you to use 3/4" thick material).
This method is also used in new-home construction when the walls will exceed a certain height or the framing will extend above a ceiling (happens in tall gable-ends sometimes.
Hope this is helpful.
Hey,
I still love this project. Hope you can retire early and do this kind of thing for fun. I will do the same and you can teach me.
I'm dying for some more commentary on national politics from you. Or are you too flummoxed by the asshatery?
Crum
Post a Comment